Welcome to b-plastic
Your partner for industry and commerce | Reliable – Competent – Innovative
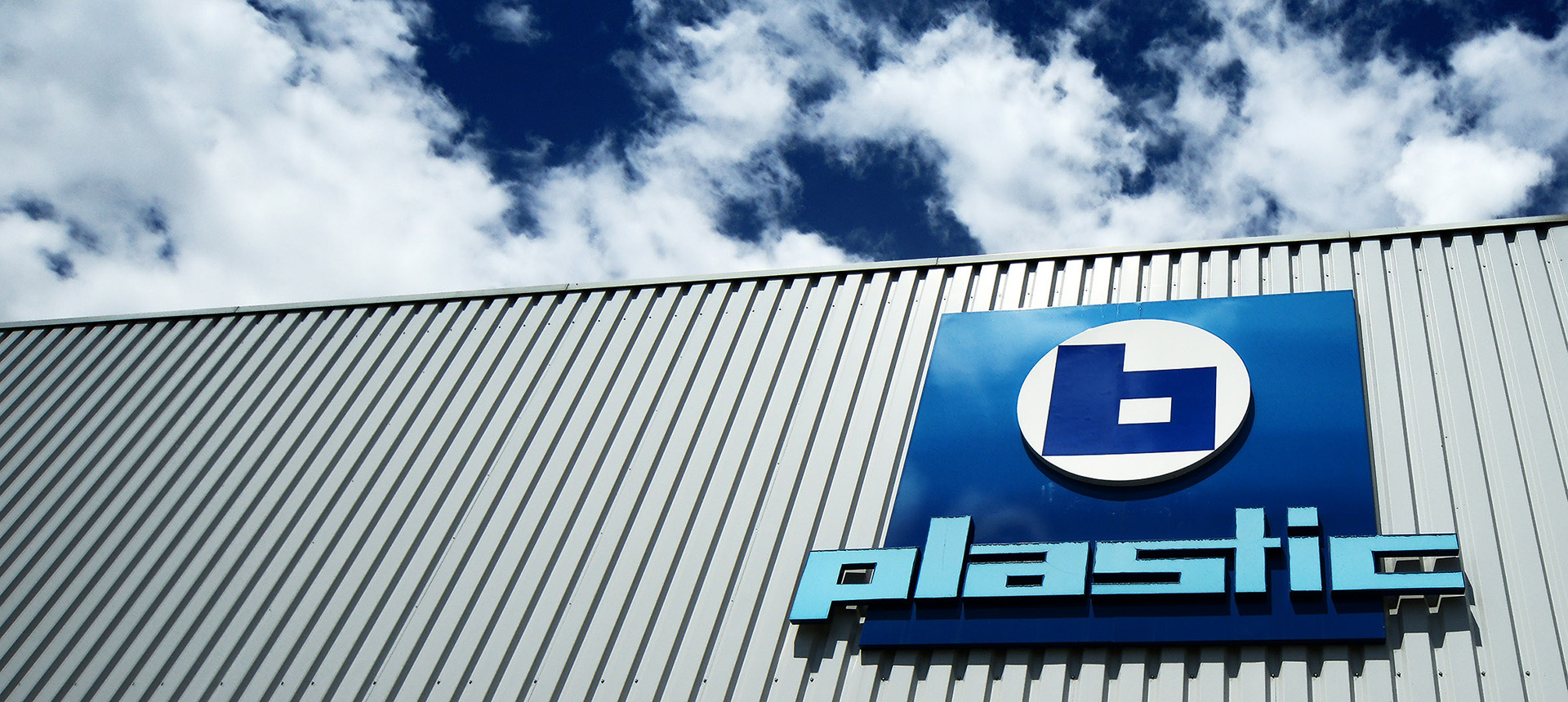
Technical plastic, metal and hybrid products
Are you looking for technical standard and norm parts or special solutions for your various applications?
With
With our team of around 50 well-trained and committed employees, we are constantly working on new ideas and concepts to improve our range of products and processes. A constant exchange of knowledge in close cooperation with our departments, the maintenance of short lines of communication and a respectful and motivated cooperation characterize our actions.
We are looking forward to your visit in our B2B store or simply to your personal call.
The many uses of our products
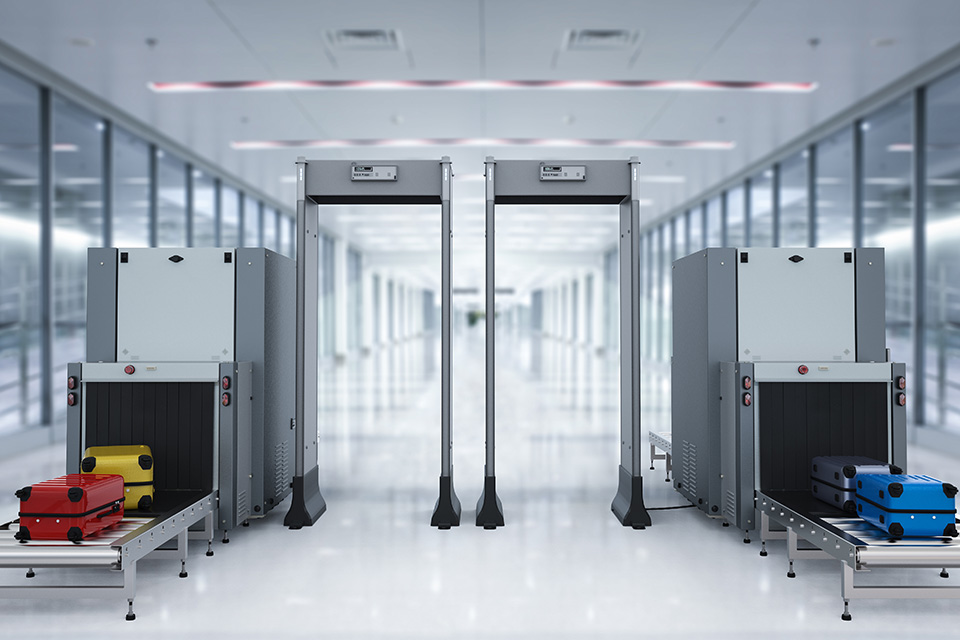
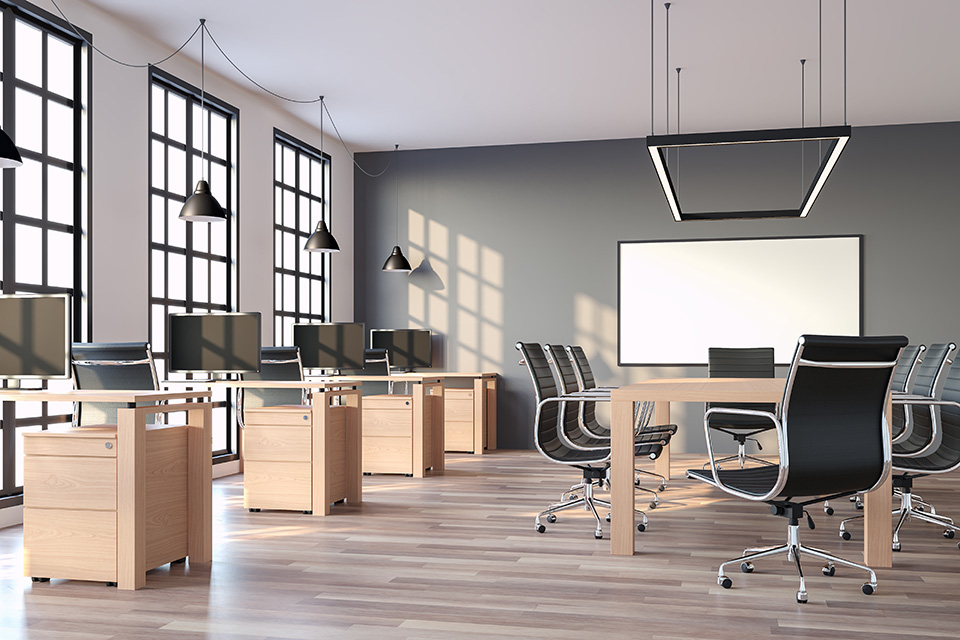
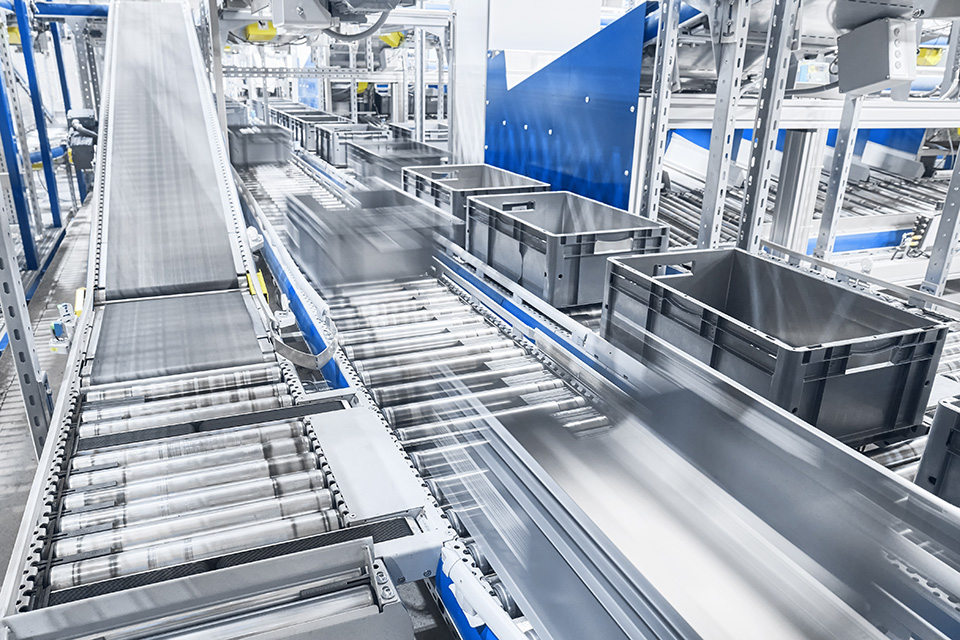
Quality, environment and compliance standards
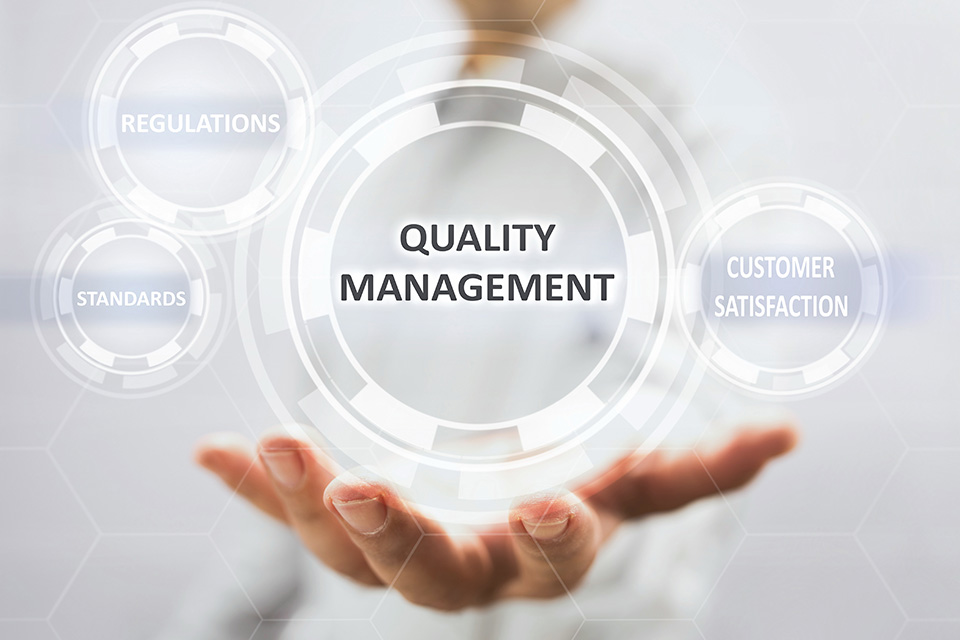
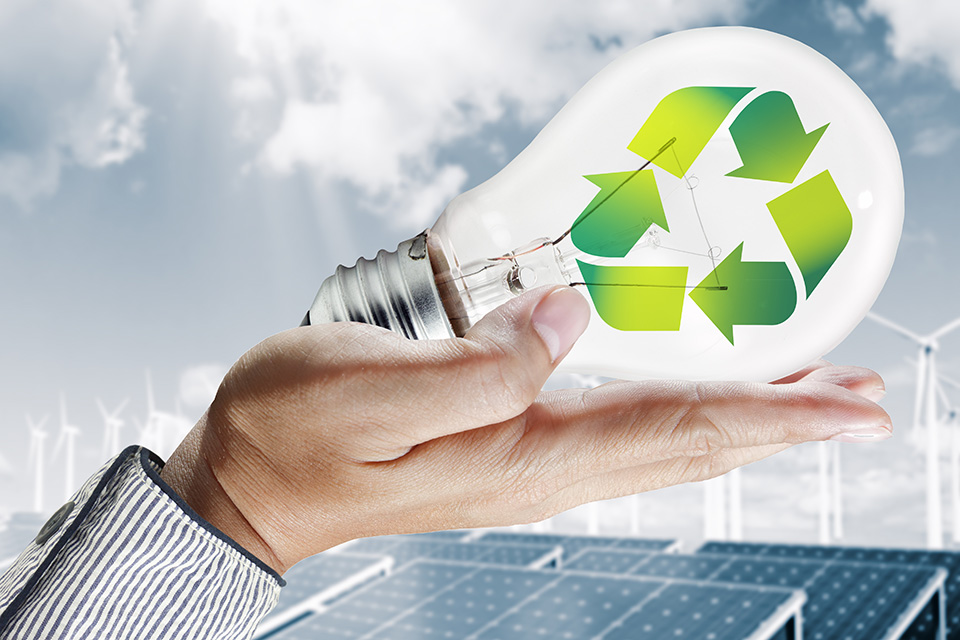
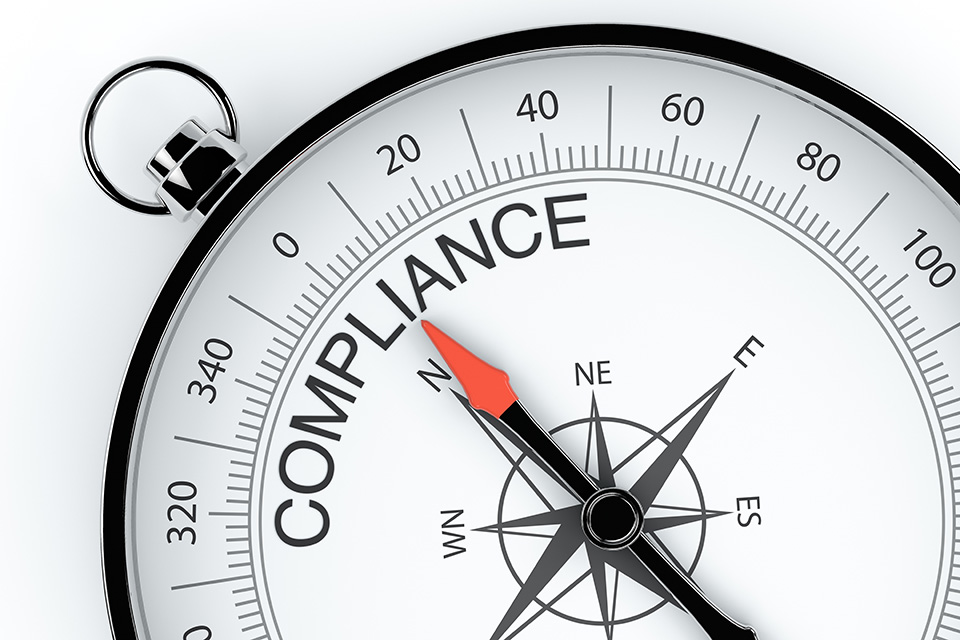
From product idea to delivery

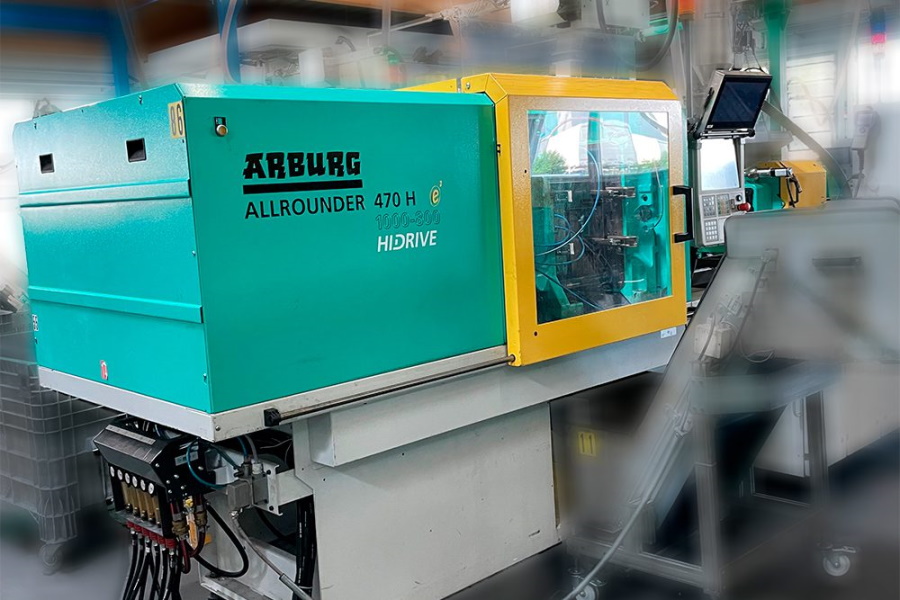
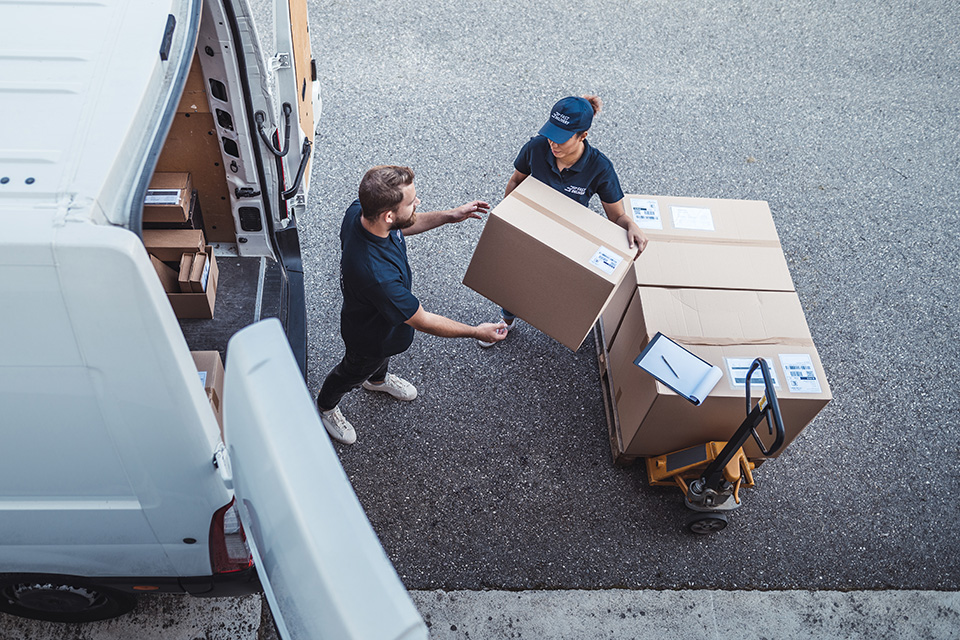