PA-Polyamide
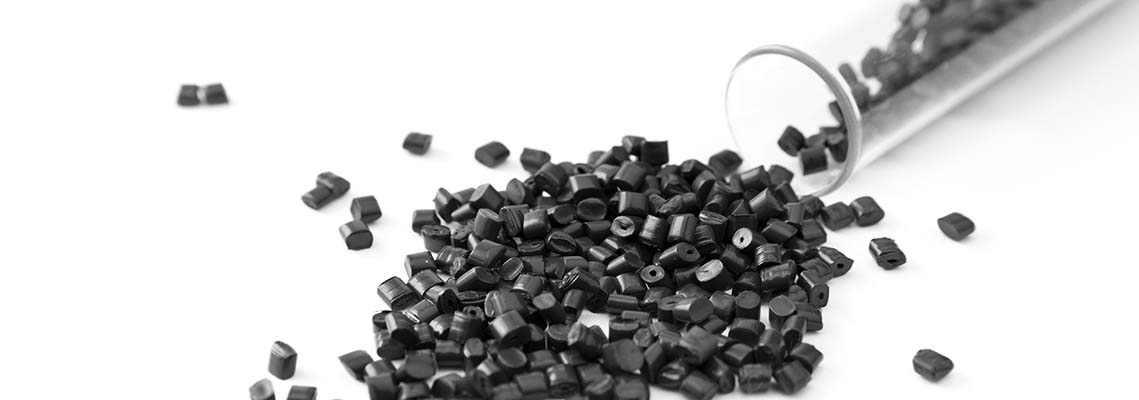
Physical – mechanical properties
Normal polyamide (1.07-1.14 g/cm³) is a medium-weight, semi-crystalline technical all-round thermoplastic. Polyamide has a relatively high water absorption (hygroscopic), which, depending on the type of polyamide and application, is adapted to the ambient climate in the factory by conditioning (warm water storage) the moulded parts, insofar as diffusion of the air humidity is not sufficient. Only then does normal polyamide exhibit its good toughness, very good notched impact strength and good stress cracking resistance (with reduced hardness and strength and with volume change/dimension change), which in many cases must already be given when the articles are assembled. Considerable strength increases can be achieved by stretching polyamide fibres:
Schematic representation of polyamide
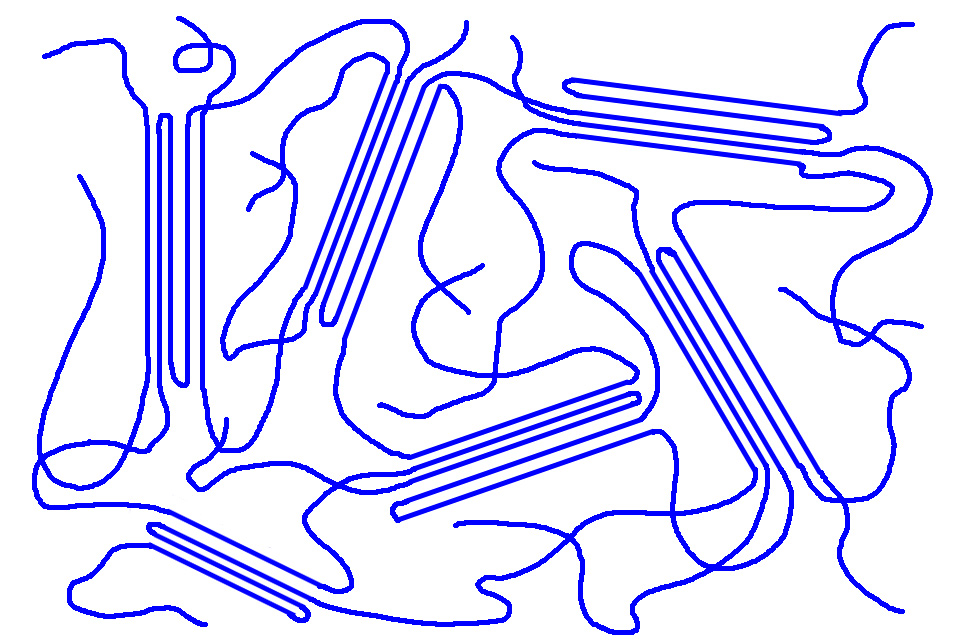
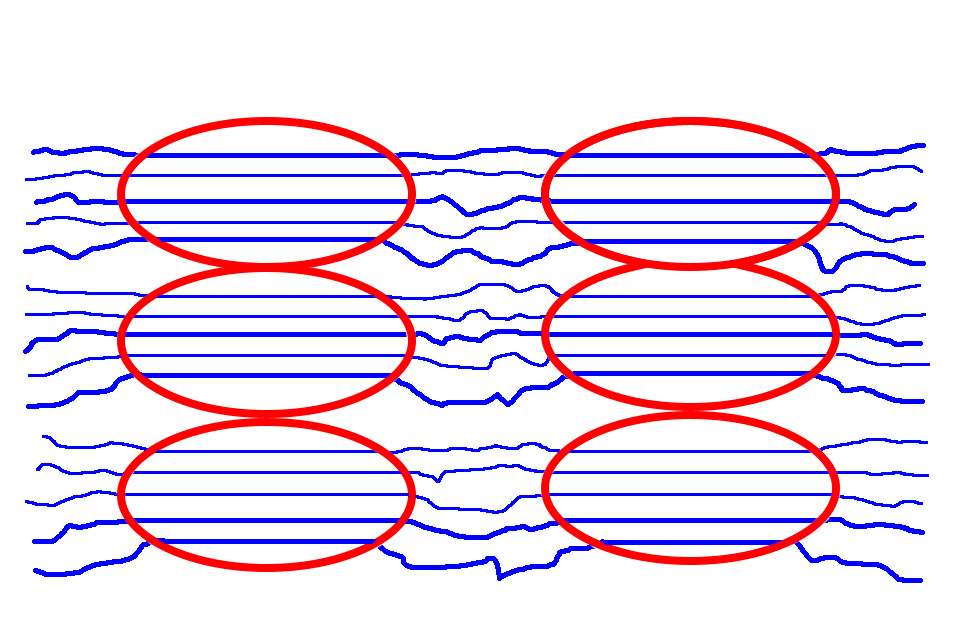
Polyamide is characterised by high creep strength, fatigue resistance, abrasion resistance and vibration damping. Glass-fibre reinforced polyamide has a higher modulus of elasticity and strength. The abrasion behaviour of polyamide is good, in bearing applications an addition of MoS2 or PTFE/silicone results in excellent sliding and emergency running behaviour.
PA can be sawn, drilled, turned, sanded, polished, welded (see thermal properties), painted and printed.
Hint:
If polyamide articles have not been stored in their original sealed packaging, but have been stored dry and warm, they should be stored in warm water for 24 – 48 h before assembly. Due to water storage, polyamide parts must not be assembled in a frozen state. The actual intrinsic temperature of the articles in the core area must be > 4 °C. Items that have reached an intrinsic temperature below 4 °C in their original packaging during transport or storage must return to a core temperature > 4 °C in their original packaging before assembly (this can take 24-48 h depending on the ambient temperature).
Optical and chemical properties
Based on the number of polar amide groups contained in their polymer chains, polyamides can be classified into the following basic types, among others: 4.6, 6, 6.6, 6.10, 11, 12.
Depending on the type, non-coloured polyamide has a yellowish-white, slightly white or watery-white inherent colour and can be coloured almost at will. Polyamide yellows due to ageing and UV irradiation. Therefore, long-term colour consistency is usually not given for natural-coloured articles.
With increasing crystallinity, polyamide shows good resistance to aliphatic and aromatic hydrocarbons, petrol, oils, fats, some alcohols, esters, ketones ethers, organic and inorganic bases up to medium concentrations, chlorinated hydrocarbons such as carbon tetrachloride, Freon, Frigen, as well as paints and varnishes. Chloroform and methylene chloride cause strong swelling. Alcohols such as methanol and ethanol have a similar effect to water or seawater (slight swelling, slight reduction in mechanical strength). PA is not resistant to solutions of oxidising agents, mineral acids, formic acid, strong alkalis, phenols, cresols and glycols.
Weather and age resistance
Polyamide is sufficiently resistant to ageing and weathering. For outdoor applications, the resistance can be increased by selective colouring, e.g. with carbon black. In the case of glass-fibre reinforced polyamide, the increase in surface area caused by the glass fibres results in greater stress on the outer surfaces, but this does not have a significant effect on the mechanical properties. The addition of suitable UV stabilisers (HALS*) can sufficiently stabilise the exterior applicability of PA mouldings with any colouring for decades.
*) = HALS (hindered amine light stabilizer) do not absorb UV radiation, but inhibit polymer degradation by continuous and cyclic removal of radicals generated by photooxidation of the polymer.
Special settings and product areas
Glass fibres and other strength-increasing fillers, MoS2 and PTFE/Si for very good sliding behaviour, various stabilisers, conductive materials to improve electrical conductivity – fibres, fabrics, tubes, screws, nuts, washers, gear wheels, door and furniture fittings, plain bearings, sliding elements, bearing bushes, fan wheels, pump housings, filter bodies.
Thermal properties
PA 6 and PA 6.6 are cold-resistant to at least -30 °C and permanent heat-resistant to a maximum of +105 °C, PA 6.6 to a maximum of +120 °C. PA 11 and PA 12 are cold-resistant to at least -50 °C and permanently heat-resistant to a maximum of +80 °C. By adding stabilisers and plasticisers, the cold or heat resistance can be increased to values of -60 °C or +110 °C, and up to 160 °C for short periods. Glow properties and heat resistance are good with normal polyamide. Glass fibre-reinforced polyamide is moderately flammable due to the wicking effect of the glass fibres. The heat resistance is even better than that of unreinforced polyamide. Even under increasing heat, polyamide is characterised by its good dimensional stability. The expansion of glass-fibre reinforced polyamide is even lower. Depending on the load and the shape of the articles, they can be exposed to continuous service temperatures between approx. -40°C and 80-120°C. Polyamide starts to decompose above 300°C. Ignition occurs from approx. 450-500°C. It burns weakly with a distinct odour of burnt horn and drips with a crackling sound, draws threads and usually extinguishes after a short time. Polyamide 6 can also withstand temperatures of up to 200°C for a short time and polyamide 6.6 with 50% glass fibres can even withstand temperatures of up to 250°C for a short time.
Physiological and joining behaviour
In case of prolonged exposure to heat, contact with food containing water is a concern. Dry, unreinforced injection moulded parts made of polyamide can be welded well and with high strength by ultrasonic welding, friction or vibration welding and hot plate welding. Moisture and glass fibres reduce the welding quality. Solvents, phenol- or resorcinol-based lacquers, concentrated formic acid, pressure-sensitive adhesives and cyanate adhesives are particularly suitable for bonding polyamide.
Examples of use
Power tool housings, housing material for electronic components, filter and pump housings, special seals, drive belts, plain bearings, gear wheels, rollers, screws and nuts.
At b-plastic, the following product groups are manufactured from PA: