PE – Polyethylene
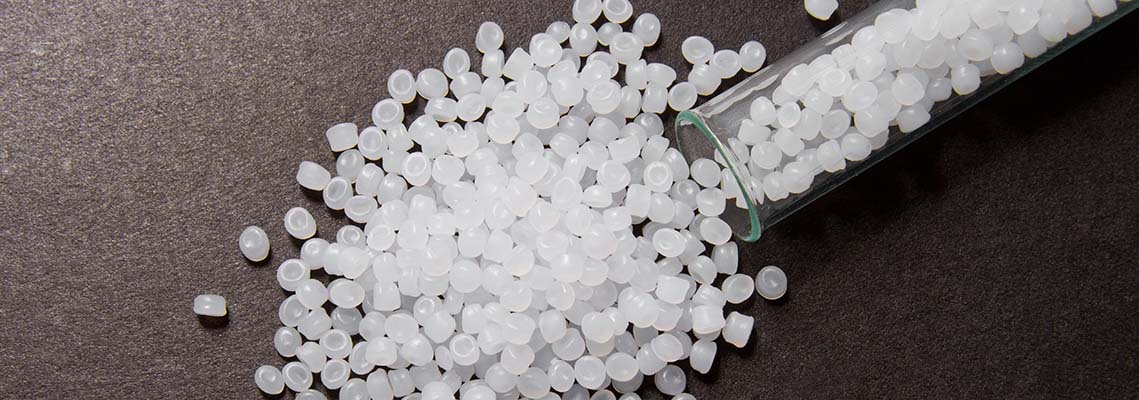
Physical – mechanical properties
With 0.90-0.96 g/cm³, PE is a very light semi-crystalline thermoplastic from the class of polyolefins, whereby VLD= Very Low Density ~0.90 g/cm³ and HD= High Density ~0.96 g/cm³ limit the density range. PE is water-repellent (hydrophobic) in normal settings like most polyolefins. PE is very tough. The modulus of elasticity, tensile strength and surface hardness give low values, increasing from VLD-PE to HD-PE. Good resistance to expansion cracking is predominantly found in VLD-PE and LLD/MLD-PE. With increasing density, increasing melt index and increasing part wall thickness, PE becomes more sensitive to expansion cracking. For appropriately stressed parts made of HD-PE (selection due to hardness and strength), care must be taken to ensure sufficiently low wall thicknesses and a HD-PE with a low melt index and low density must be selected.
Optical and chemical properties
Natural-coloured PE is translucent. With decreasing wall thickness, PE moulded parts become more transparent. VLD/LLD-PE moulded parts have a very good glossy surface with appropriately designed injection moulds. Naturally coloured PE mouldings are UV-sensitive and yellow with time. PE mouldings have a non-polar surface that is only attacked by a few chemicals. PE is resistant to acids, alkalis, alcohols, oil and salt solutions. In addition, HD-PE is resistant to petrol. VLD-PE and LD-PE swell in aliphatic and aromatic hydrocarbons. PE is not resistant to strong oxidising agents (e.g. nitric acid). Water vapour permeability is low, gas permeability is quite high compared to other plastics.
Resistance to weathering and ageing
PE is sufficiently resistant to irradiation in the visible range. UV radiation causes oxidation of the surface of PE mouldings. This is intensified by the presence of oxygen and therefore leads to brittleness and long-term disintegration. Suitable colouring, e.g. with carbon black, stabilises but reduces the heat ageing resistance. The addition of suitable UV stabilisers (HALS*) can sufficiently stabilise the outdoor applicability of PE mouldings with any colouring for decades.
*) = HALS (English -hindered amine light stabilizer) do not absorb UV radiation, but inhibit polymer degradation by continuous and cyclic removal of radicals generated by photooxidation of the polymer.
Special settings – product areas
Fillers to further reduce the cost of the material, various stabilisers, admixture of PE-based elastomeric thermoplastics (TPO) for softer and tougher settings – transport containers, washers, pipe plugs, furniture fittings, disposable articles, substitution of soft PVC with VLD-PE for highly elastic moulded parts.
Thermal properties
The continuous service temperature of PE without mechanical stress is approx. -50 to 80°C for VLD-PE, -50 to ~95°C for LD-PE and -50 to 105°C for HD-PE. Ignition occurs from approx. 340°C. PE also burns outside the flame, glowing weakly with a strong waxy odour and dripping off as it burns.
Physiological and joining behaviour
PE is physiologically harmless as long as no additives are used that could be harmful to health. Some manufacturers also certify food compatibility. Due to the good chemical resistance resulting from polar moulded part surfaces, only pressure-sensitive adhesives can be used. For this purpose, the moulding surface must be thoroughly roughened and primed. The former can also be achieved by scarfing and corona discharge. If possible, gluing and painting should be avoided. PE can be joined by hot plate, friction, vibration or hot gas welding.
Examples of use
Production of packaging films for books, paper handkerchiefs, etc., as well as carrier bags. Production of molded parts such as kitchen bowls, cutting boards.
At b-plastic the following product groups, among others, are manufactured from PE:
Category Plugs: GL, VL,, SRL, SFL. OVL, CGM, GLAF, VLAF/Q, VLAF/R
Category Furniture glides: GLK, GLM, MGS, OVLSF, RS, SPOZ, XGF, XGK, WL